The Future Of Fleets: AI Predictive Maintenance Prevents Breakdowns
AI-driven predictive maintenance has proven to be highly effective in saving waste fleets up to $2500 per truck annually. By leveraging advanced technology, this approach can prevent 50% of breakdowns, ultimately increasing truck uptime and operational efficiency. This proactive maintenance strategy helps identify potential issues before they escalate, leading to significant cost savings and improved fleet performance. Implementing AI-driven predictive maintenance can revolutionize how waste fleets manage their vehicles and resources, resulting in a more sustainable and profitable operation. The success of this approach highlights the importance of integrating innovative solutions into traditional fleet management practices.
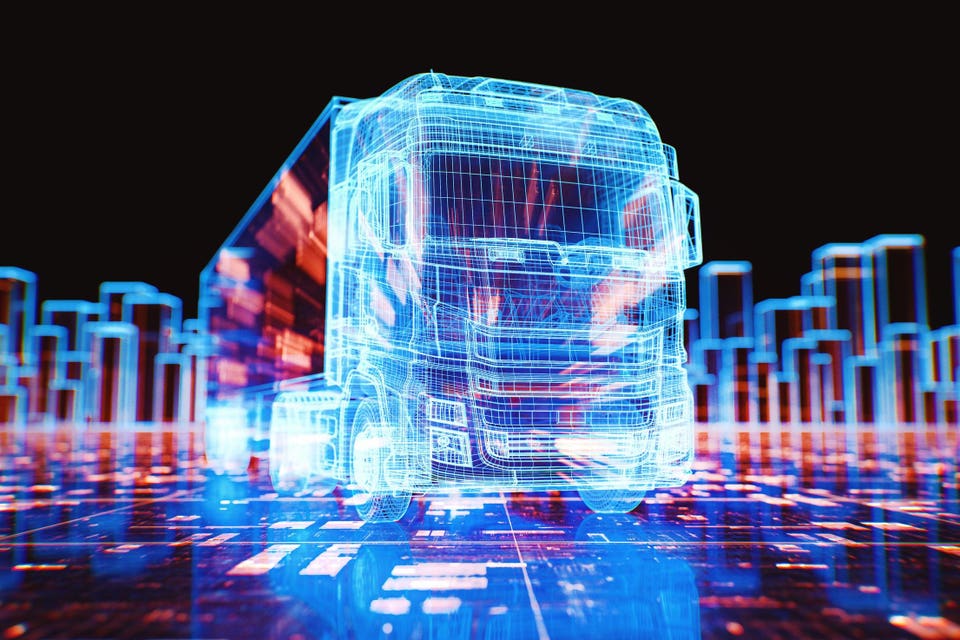
The waste collection industry generated $69 billion in revenue in 2024, accounting for over two-thirds of the total US waste and recycling revenue. Logistics is the cornerstone of this industry, given its heavy reliance on trucks to deliver essential services. Nearly 180,000 refuse trucks operate across the United States six to seven days a week, making over 1,000 stops every day. These vehicles endure punishing schedules and rough conditions daily, making breakdowns common and very costly. When a garbage truck breaks down, missed pickups ripple across neighborhoods, complaints surge, and emergency logistics drive costs higher. Each day of downtime directly cuts productivity and erodes service reliability.
Challenges in Fleet Maintenance
“I face downtime daily,” says Michael Laskowski, director of asset and fleet of Austin Wood Recycling. He told me, “Downtime is devastating because it’s a hidden cost that is easily ignored. It’s not only the loss of that equipment, but the serious impact it has on your overall production schedule.” Garbage trucks frequently fail due to their extreme duty cycles. Stopping and starting hundreds of times daily, and exposure to corrosive waste put immense strain on mechanical systems such as brakes, hydraulics, and transmissions. Average annual breakdown costs exceed $5,000 per truck, and roadside repairs can be up to four times more expensive than shop-based maintenance. Beyond direct expenses, breakdowns cause labor overtime, rerouting, delayed pickups, and missed service-level agreements. Not surprisingly, this is the top factor that keeps fleet managers awake at night.
Addressing Downtime with Predictive Maintenance
One of the major contributors to downtime is the parts unavailability when they are urgently needed. Without visibility into component wear, managers face unexpected shortages at critical moments, forcing costly emergency procurements, limited vendor choice and shipping delays. A city fleet audit revealed only 21% of requested parts were available timely, while nearly 40% took more than 48 hours to arrive. These delays stall repairs, keeping trucks idle and costing fleets valuable uptime. Inconsistent repair quality frequently disrupts fleet operations. The same audit referenced above indicated that 24% repairs on Class 8 vehicles, such as garbage trucks, failed within 60 days. These vehicles made an average of 16 trips to the garage each year, often for the same problem.
The Role of AI in Fleet Maintenance
Recent technological advances have made AI-driven fleet maintenance practical and economical. Affordable sensors, already embedded in most vehicles by manufacturers, enable continuous real-time vehicle health data access. With 5G connectivity, trucks transmit critical information even from remote locations, enabling real-time visibility into fleets. Simultaneously, machine learning algorithms have become more powerful and accessible. They detect subtle shifts in performance that human eyes or routine checks might miss. Generative AI tools can even interpret maintenance manuals, recommending clear and practical next steps that bridge technician skill gaps. Thanks to cloud platforms, predictive maintenance software can be rolled out remotely without expensive on-premise setups. Fleets of all sizes can now access these solutions quickly, affordably, and effectively, with an exceptional return on investment.
Benefits of AI in Fleet Maintenance
AI systems monitor live sensor streams across the vehicle, from vibration and temperature to pressure and fuel efficiency, to detect anomalies that signal impending failure. Targeted alerts let maintenance teams schedule proactive repairs, long before a breakdown occurs. Fleets report annual savings of up to $2,500 per truck by avoiding unplanned downtime and extending component life. This can also help prevent hazards like fires, often caused by materials like lithium batteries discarded in trash cans. Sensors such as temperature and chemical detectors could help alert operators to such risks, enhancing driver safety.
AI helps fleets move from reactive to proactive parts management. By forecasting which components are likely to fail and when, managers can order them months ahead of time, eliminating emergency purchases and premium pricing. This helps teams optimize parts inventory. AI learns from each repair by analyzing patterns in historical work orders, parts replaced, and post-repair performance. It identifies which trucks are most likely to return with the same issue and flags them for further inspection, based on repair types, technician performance and vehicle conditions.
The Future of Fleet Maintenance
Fleet maintenance across waste and other industries is undergoing a major transformation. Traditional preventative maintenance based on general heuristics is no longer enough. Technology can help monitor the health of each vehicle in real-time, anticipate issues, recommend precise fixes, and streamline parts management. The impact is real: fewer breakdowns, lower costs, and more reliable service. AI won’t replace technicians. It empowers them. Mechanics remain the decision-makers in the service shop, supported by insightful analytics. Fleet managers can prioritize actions confidently with data-backed clarity.
Imagine Truck #14’s sensor flags an anomaly mid-route on a Thursday afternoon. AI instantly predicts a belt failure within two weeks, schedules weekend maintenance, and confirms parts availability. The technician completes repairs promptly, ensuring the truck is ready by Monday morning. No missed pickups, no chaos. Just uptime and efficiency. This isn’t just the future of fleet maintenance, it’s a reality already. Fleets embracing AI today will lead the industry tomorrow.